What is FRP?
FRP is a structural composite that is perfect for industrial & infrastructure applications
Fiber-Reinforced Polymer (FRP) is an engineered material consisting of reinforcement fibers, polymer resin and additives to achieve the desired performance properties. This combination creates an extremely strong and durable material that can be used for parts inside equipment up to large, heavily loaded civil infrastructure. The type of reinforcement fiber is chosen based on the requirements of the application. For example, carbon fiber is commonly used in airplanes and recreational equipment - while the most common reinforcement material is glass fiber, given its combination of properties and cost.
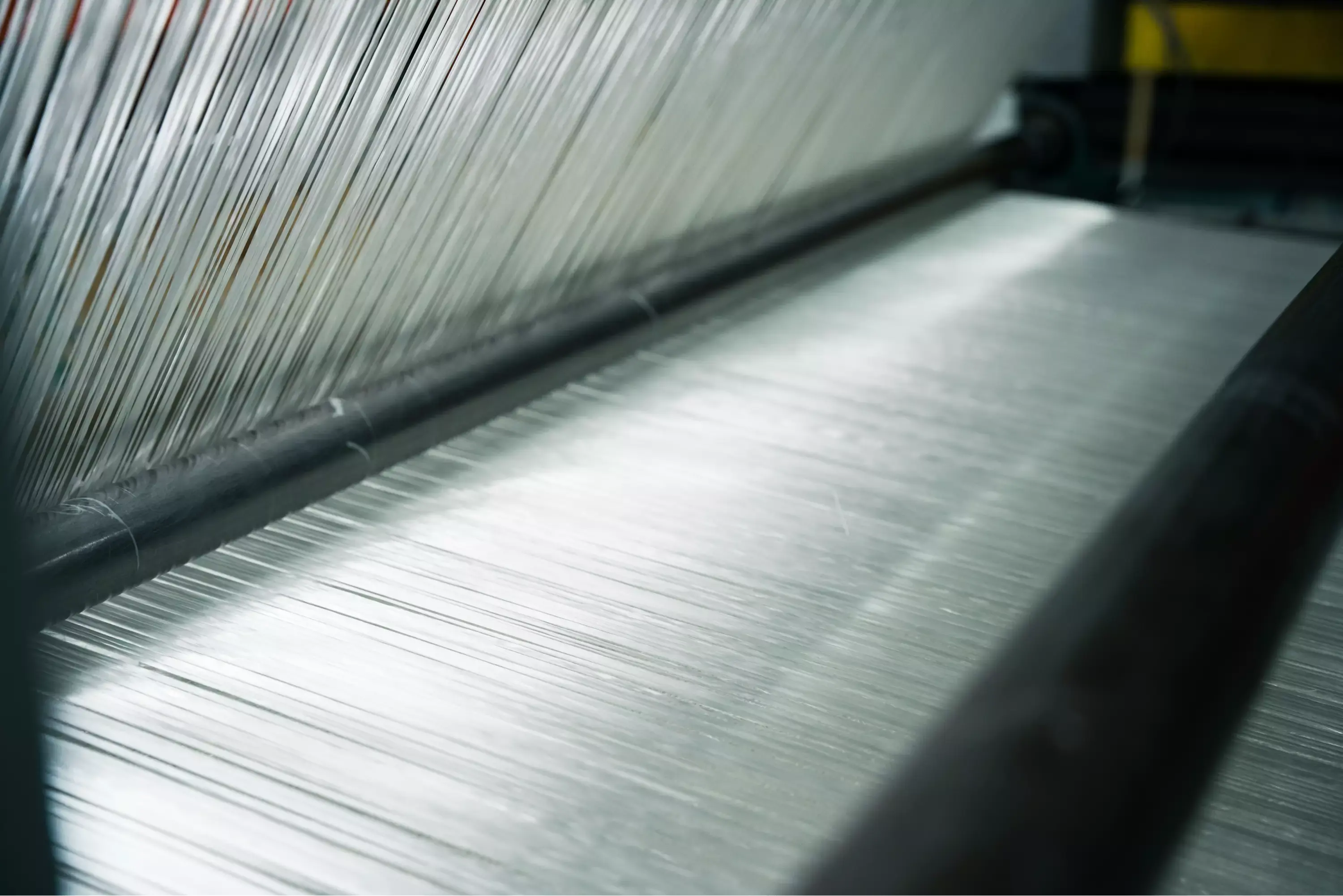
WHY FRP IS AN IDEAL CHOICE FOR A WIDE RANGE OF PRODUCTS, OFFERING:
Lightweight material
FRP components are extremely lightweight compared to other construction materials. This makes them safer, easier to work with and cheaper to transport. They also don't require as much equipment to install.
Corrosion resistance and low maintenance
FRP is extremely durable, making it suitable for heavy-duty usage in a wide range of environments. Its corrosion resistance makes FRP capable of withstanding salt, water, chemicals and other harsh weather conditions without deterioration. This means it can last for up 100 years with very little need for maintenance or rebuilds.
Cost-effective
Creative Composites Group builds our high-quality FRP components to offer long-term cost savings and profitability through its many beneficial qualities. FRP often offers lower acquisition costs compared to traditional materials.
Flexible design
FRP can be engineered to meet the exact application requirements. Factors such as size, shape, color and functional features can be customized to ensure smooth and easy installation.
Shorter production and installation time
FRP can be prefabricated, allowing crews to install each part much faster. This makes FRP ideal for construction projects in public areas that have tight timelines and limited construction hours.
BENEFITS OF FRP OVER TRADITIONAL MATERIALS
FRP VS. STEEL
- More flexibility in terms of color options and functional features
FRP VS. ALUMINUM
FRP VS. WOOD
FRP VS. CONCRETE
CREATIVE COMPOSITES GROUP ENSURES YOUR FRP PROJECT SUCCESS
FRP is a strong, durable, lightweight and corrosion-resistant alternative to traditional construction materials. At Creative Composites Group, we are a leader in designing and manufacturing FRP composite products. Our combined team of experts offers innovative FRP solutions designed to meet the specifications and requirements for a wide range of applications. To learn more about the benefits, products, and applications of FRP download our FRP Products & Capabilities Brochure today.